E100
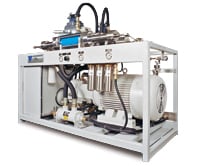
E100
The E100 is the powerhouse of the WSI pump family. Producing a 2 gallon per minute (gpm) flow rate at maximum pressure, it is powerful enough to reliably drive any cutting application while utilizing from 1 to 4 abrasive cutting heads.
Specifications
Maximum Operating Pressure:
- 60,000 psi (4,140 bars)
High-Pressure Flow Rate:
- 2.00 gpm (7.56 lpm)
Intensifier Cycle Rate:
- 22 cycles/min. at max. flow rate
Electrical System:
- Main Motor: 50 hp / 74 kW (TEFC)
- 208v / 3 ph. / 60 Hz
- 230v / 3 ph. / 60 Hz
- 460v / 3 ph. / 60 Hz
- 190v / 3 ph. / 50 Hz
- 380v / 3 ph. / 50 Hz
- Booster Pump Motor 1/2 hp/0.37 kW (TEFC)
- 120v/1 ph./60Hz
- 208v/1 ph./60Hz
- 230v/1 ph./60Hz
- Controls:
- 120 VAC / 24 VDC
- Safety Shutdown Circuits:
- High Oil Temperature
- Low Oil Level
- Low Water Pressure
- Intensifier Over-speed
- Intensifier Stall
Hydraulic System:
- 8.5 cu. in. (140 cu. cm) Piston Pump
Max. Operating Pressure: 3,000 psi (207 bars)
Cooling Water Flow Rate: 4 gpm (15.5 lpm)
Low Pressure Cutting Water System:
- Optimum Inlet Pressure: 65 psi (4.50 bars)
Booster Pump Setting: 225 psi (15.5 bars))
Orifice Capacity at 55,000 psi (3,800 bars):
- Quantity / Orifice Diameter
- 1 – 0.021 in. (0.53 mm)
- 2 – 0.014 in. (0.35 mm)
- 4 – 0.010 in. (0.25 mm)
- 8 – 0.007 in. (0.17 mm)
Physical Dimensions:
- Height: 64 inches (1.62 meters)
- Width: 36 inches (0.91 meter)
- Length: 80 inches (2 meters)
- Weight: 4,500 pounds (2,041 kg)
Features and Advantages
- Proven, heavy-duty, industrial, high-pressure intensifier with ceramic plungers.
- Slow intensifier speed – 22 cycles/minute. This slow speed both reduces the number of pressure spikes in the system and reduces the number of pressure reversals. This slow speed virtually doubles the fatigue life as compared to other waterjet pumps.
- Patented “DuraCheck” check valves utilize replaceable seats on both ends of the check valve. This technology, offered only by WSI, greatly extends check valve operational life as it isolates and protects the expensive check valve body from damage.
- One large (6″ OD) accumulator insures low pulsations in the high-pressure system.
- A pneumatic bleed-down assembly provides for depressurization of the high-pressure system immediately upon shutdown.
- All high-pressure tubing and fittings are Autoclave.
- A PLC control panel monitors the system. The control panel includes:
- Allen-Bradley Micrologix processor
- shutdown enunciators
- emergency shutdown
- motor starter, overload relay, and disconnect in 460V US models
- Highly reliable proximity switches control the sequencing of the intensifier.
- Oversized, low-load motor.
- The motor is mounted on high load isolators to reduce noise and vibrations.
- Low hydraulic oil pressure – 3,000 psi / 207 bars.
- A dial, main compensator allows for simple control of the cutting water pressure.
- A dual compensator provides lower, alternative, preset cutting pressures for tasks such as piercing or drilling.
- The unit has a hydraulic oil cooling system with a full-flow oil heat exchanger.
- The oil reservoir has two access doors for easy maintenance.
- There is an inlet, cutting water, booster pump included in the unit. This insures that the high-pressure cylinders are fully charged and eliminates the extra expense of a separate booster pump.
- Brass fittings are used on the entire inlet water system to protect against corrosion.
- Differential pressure gauges across the water filters are included to help indicate filter replacement. (Water filtration to 10, 5, and 1 micron)
- There is a full-flow hydraulic oil filter, with indicator, to insure clean oil and protect the system.
- The frame is constructed from 2″ X 3″ structural steel, box beams. All welds are full welds. No tack welding is used.